Devices for the world’s best radio telescopes
At the institute’s mechanical workshop & design unit, IRAM engineers, engineering draftsmen and mechanics work together on the design and manufacturing of mechanical devices for radio telescopes at millimeter wavelengths as well as their receiver systems.
Once the cosmic signal is collected by the radio antenna, it is focused inside the antenna and onto the receiver system, where it reaches the horn and is channelled through a narrow, millimeter-sized conduit called the wave-guide, before reaching the mixer block, a device only a few centimeters in size.
Horn, wave-guide and the mixer block (which contains the superconducting device) are high-precision components and each of them is absolutely crucial for a smooth transmission and the further processing of the cosmic signal. Their design and production is at the core of the mechanical group’s challenging mission.
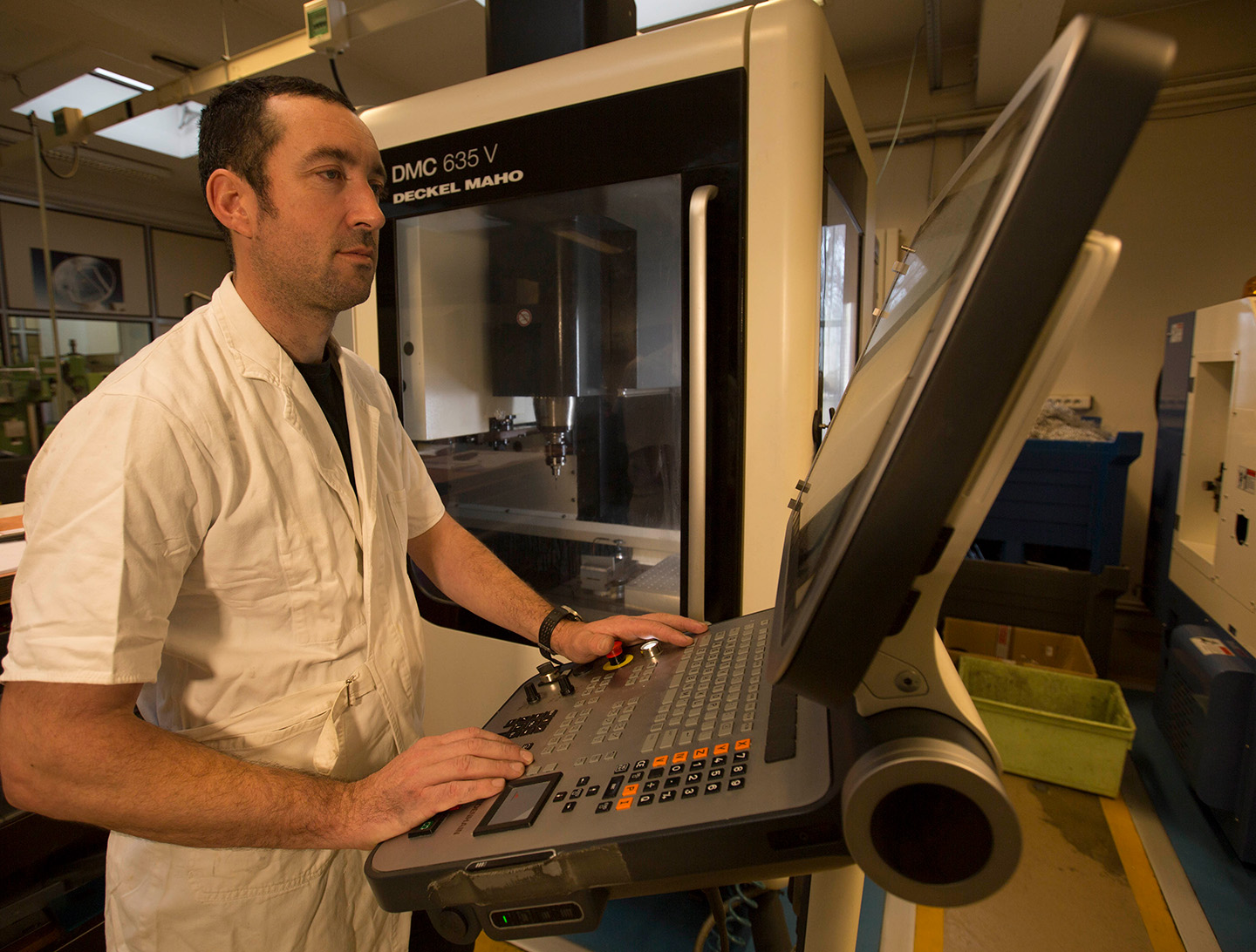
The complex pre-production process includes studying an ideal ‘signal path’ using highly specialized design software and 3-D drawings. In close collaboration with IRAM’s receiver system engineers the group determines specific and required performances, like the wave-guide’s width, the type of grooving to be used, its tolerated depth, width and localization, the constraints of mass and the limits of tolerance for the actual manufacturing process.
Having completed the technical studies, the mechanical group’s engineers start to design the devices with a special CAD-software.
Before the devices are produced, they have to undergo various technical control procedures. Using micro mechanical manufacturing technologies, the devices are manufactured in-house at the institute’s mechanical workshop, controlled, and then finally assembled at the IRAM receiver systems laboratories.
Designing the NOEMA antennas
The mechanical group is also partly responsible for the NOEMA antennas at the Plateau de Bure. The group is in charge of the design and construction of the 15-meter in diameter high-precision antennas. It assists the observatory’s staff during the maintenance period in summer and keeps optimising the antennas’ performance.
An example for the workshop’s expertise is the manufacturing of the antennas’ aluminum panels: The panels are milled by a numerically controlled machine and then stress-relieved in order to obtain an extremely high-precision surface. With their know-how, IRAM engineers are able to achieve a surface precision of about 20 microns for 1.5 square meters (which is less than the width of a human hair)!
Housings for IT modules and electronic chips
Another field of activity is the design and the manufacturing of housings for IT modules and electronic chips. Therefore, the mechanical workshop is also equipped with several conventional machines which are not – like all the other machines at the workshop – digitally controllable. The group has its own network of subcontractors for prototypes.
Although this activity is only subsidiary, the mechanical group is able to respond flexibly and adapt quickly to those demands.
State-of-the-art equipment
The mechanical workshop’s production facilities and high-precision machining processes enable IRAM engineers and technicians to manufacture high-precision devices, from complex components of prototypes to small serial productions.
The IRAM workshop is equipped with the latest generation of CNC lathes and milling machines and non-contact measuring microscopes. In terms of measuring and quality control all these equipments are state-of-the-art facilities.
Learn more about our work
Our latest updates
Explore all the latest news from our research and technology groups and never miss out on important upcoming events.